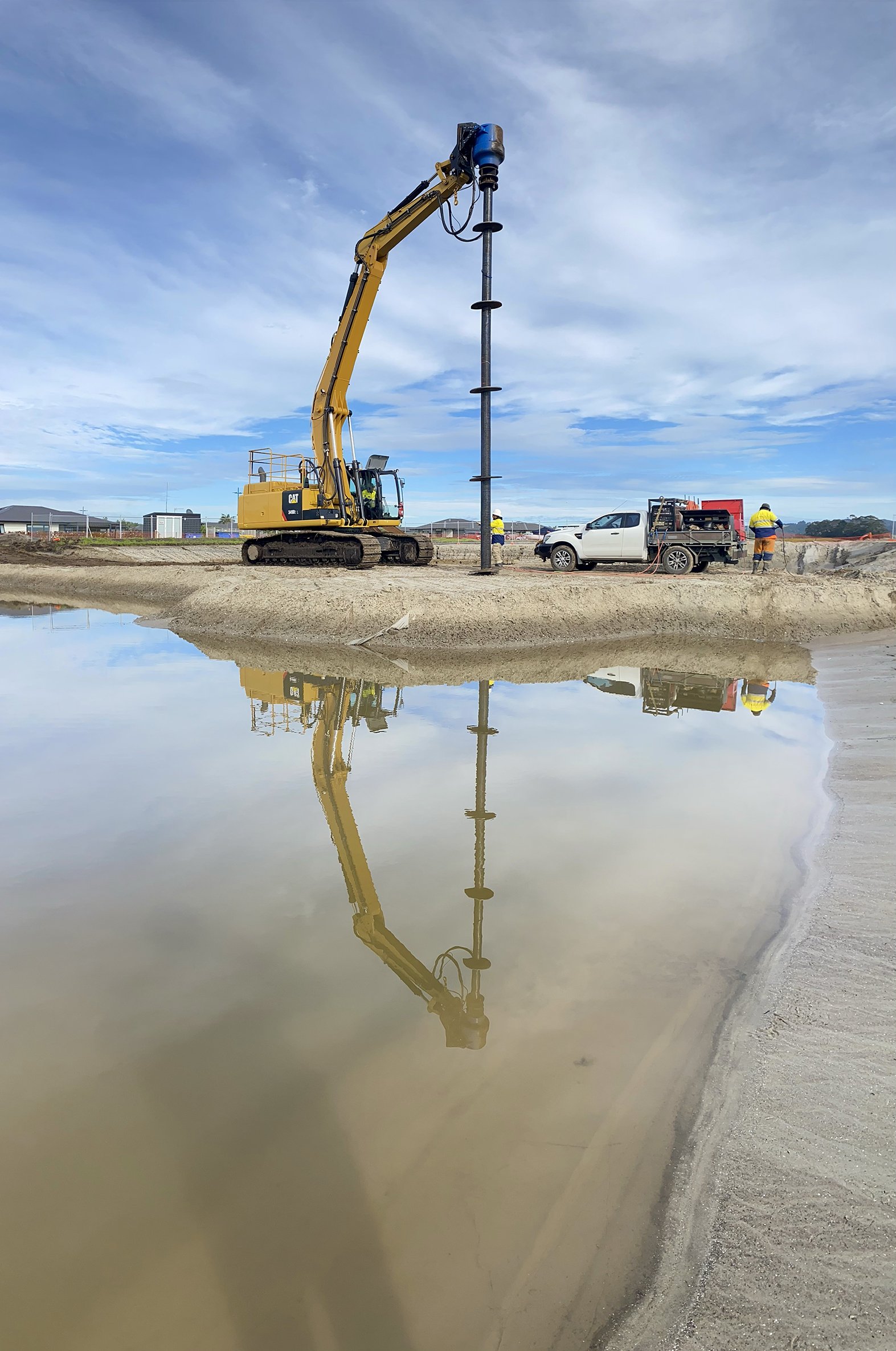
WHY USE SCREW PILES?
WHAT IS A SCREW PILE?
Screw piles are often referred to as helical piles in the northern hemisphere. This is because they have an oversized helix that is the predominant feature of the pile.
Put simply, a screw pile is a CHS pipe that has a large helix welded to the bottom. The helix is then rotated (or screwed) into the ground until it reaches the geotechnical strata it was designed to embed into.
Designers will utilize different diameters and thicknesses of the CHS pipe, as well as changing the helix diameter and thickness – and even how many helices are placed on the pipe. The most we’ve used is 8 helices, but typically you only need 1 to 2 helices per pile.
WHY SCREW PILES?
Screw piling is one choice of foundation methodology. When choosing to screw pile, you are comparing it to the other methods, and then essentially completing a SWOT analysis (Strengths, Weaknesses, Opportunity, and Threats (or risks!)). By completing this analysis, you essentially boil everything back to the following:
Will the method be able to achieve the engineering requirements?
This is a relatively binary question. Yes or no.What is the upfront cost?
What will be the likely end cost when you factor in possible risks as well the opportunities with value engineering the system as a whole?
This will allow the client and consultants to make the best decision for their project.
Everything will always come back to COST ($$$$$) and PROGRAMME (days on critical path). Depending on the geotechnical conditions and pile loads – we have seen screw piles save months on programme and millions of dollars on the project bottom line!
what should i consider when choosing screw piles?
When choosing to screw pile (instead of another foundation methodology), you always need to be clear on the following three key elements:
PILE LOADS:
A screw pile can achieve (currently) up to 5,700kN compression (ultimate capacity) and over 3,000kN tension.
But they can be economic for lightly loaded piles, even as little as 50kN.
Lateral loads were the Archilles Heal of screw piles, but we can design piles to achieve in the order of 200kN per pile, and as much as 800kN when using in combination with overbores. Lateral is no longer the reason not to use screw piles.
Being clear on the pile loads will help determine if screw piles are feasible, or optimal.
GEOTECHNICAL OR GEOLOGY:
What are the screw piles being installed through? (the upper layers),
What material is the helix founding in?
What depths?
Good geotechnical reports help us to instantly determine if screw piles are feasible (YES/NO), let alone the best methodology.
THE SITE ENVIRONS:
Are you piling beside a water course? (environmental constraints with spoil, cement, or drilling fluids)
Is there vibration / impact restraints? (like a substation, or heritage building)
Head height restrictions? (like retrofitting a building, or piling underneath a powerline)
Limited access/egress onto the site? (large plant can’t get onsite, or can’t manouevring within it, or restricted material deliveries.)
Speed is paramount? (Block of line? Or night work?)
These are just some of the questions we ask ourselves when determining the suitability of screw piles – so it’s not a black-and-white scenario with a clear answer.
what goes on screw piles?
Basically anything can go on a screw pile.
Typically Medium / Large Commercial Structures:
When the loads become too big for micro-piles, and timber piles – then screw piles, with a larger load capacity, might be better.
Examples might be:
retirement homes
apartment blocks
large commercial
schools
hospitals
data centres
airports.
Infrastructure and Industrial:
While infrstructure typically have higher loads, screw piles can be just the trick you need because of the installation benefits.
Examples might be:
tanks & pump stations
pipelines & pipe-bridges
rail/bus stations
light poles, gantry poles, catenary poles.
Oil & Gas, Electrical, Industrial:
Any structure you need for your important plant – but where you can’t afford to have the plant shutdown while construction occurs. This is where no ground disturbance and no vibration are a huge benefit!
Examples might include:
transmission towers
substations.
Renewable Energy:
Every structure requires a foundation. When in remote locations, a key benefit of a screw piling is that you don’t need large volumes of concrete.
Examples might include:
solar farms
wind farms.
Anchors:
A screw pile is essentially, also, a tension pile. As the helix is purpose built to provide superior tension capacity, a screw pile will often be shorter in length than a soil nail while still achieving the same load or greater. This may help avoid issues with boundary lines.
Examples might include:
anchors for a retaining wall
tie backs for guy-wires.
so when is screw piling best?
Every project is different – when you consider the variables of 1) pile loads, 2) geotechnical conditions, and 3) site environs. Screw piling is never a silver bullet – but there are scenarios where it is definitely more favourable.
Deeper is better!
Going deeper for other piling methods requires much larger plant (cranes and drilling rigs) and it then becomes slower.
With a screw pile, a lot of money goes in to pressing and welding the helix, but thereafter we simply splice pipe as we go deeper.
Our team regularly install piles to depths of 36m-40m deep. We have installed piles as deep as 50m!
Poorer soils are better!
This sounds like a misnomer, but there are clear reasons.
Collapsing soils are harder for bored piles (think temporary casings, polymer / bentonite)… Screw piles effectively have a permanent casings.
Liquefiable soils result in negative skin friction – increasing the load on skin friction based piles like bored piles and driven piles. Screw piles are predominantly end-bearing with a slimmer shaft – so attract less load.
Tension!
A bored pile requires longer “rock sockets” often with a bell or grooving.
A driven UC can often struggle to penetrate sufficiently into the rock, or you have to upsize the pile to take the impact of the drive hammer without deforming.
A screw pile doesn’t have to penetrate much beyond with 1-2m to achieve sizeable tension loads. Or we just add more helices.
TORQUE MATTERS
Similar to the mantra of property investing (location, location, location) – screw piling is all about torque! Some wise people have even said it shouldn’t be called “screw piling” but “torque piling”.
Why?
Having screw piles consistently achieve the design loads is not just about putting an auger motor on an excavator and ‘screwing’ a piece of pipe into the ground.
To get a piece of pipe into the ground it is all about the torque that can be applied to the pile shaft.
Torque is then used to confirm that the pile is in the proposed founding strata as identified in the geotechnical report.
Finally, the final installation torque verifies the achievable pile capacity in correlation with sustained static load testing information.
The most common cause of screw piles failures is because designers and contractors are unaware of the true value of torque!